The Science Behind Porosity: A Comprehensive Overview for Welders and Fabricators
Recognizing the detailed systems behind porosity in welding is crucial for welders and fabricators pursuing remarkable craftsmanship. As metalworkers explore the depths of this sensation, they reveal a globe governed by various factors that influence the development of these minuscule gaps within welds. From the structure of the base products to the details of the welding process itself, a wide variety of variables conspire to either worsen or minimize the visibility of porosity. In this thorough overview, we will certainly decipher the scientific research behind porosity, exploring its impacts on weld high quality and introduction advanced techniques for its control. Join us on this journey via the microcosm of welding blemishes, where accuracy fulfills understanding in the search of remarkable welds.
Comprehending Porosity in Welding
FIRST SENTENCE:
Exam of porosity in welding reveals vital understandings into the stability and high quality of the weld joint. Porosity, identified by the presence of tooth cavities or spaces within the weld steel, is a typical worry in welding processes. These gaps, otherwise properly addressed, can endanger the structural integrity and mechanical residential properties of the weld, bring about potential failures in the completed item.

To identify and measure porosity, non-destructive testing methods such as ultrasonic testing or X-ray evaluation are typically utilized. These techniques permit the recognition of interior problems without jeopardizing the integrity of the weld. By analyzing the dimension, shape, and distribution of porosity within a weld, welders can make educated choices to enhance their welding processes and achieve sounder weld joints.
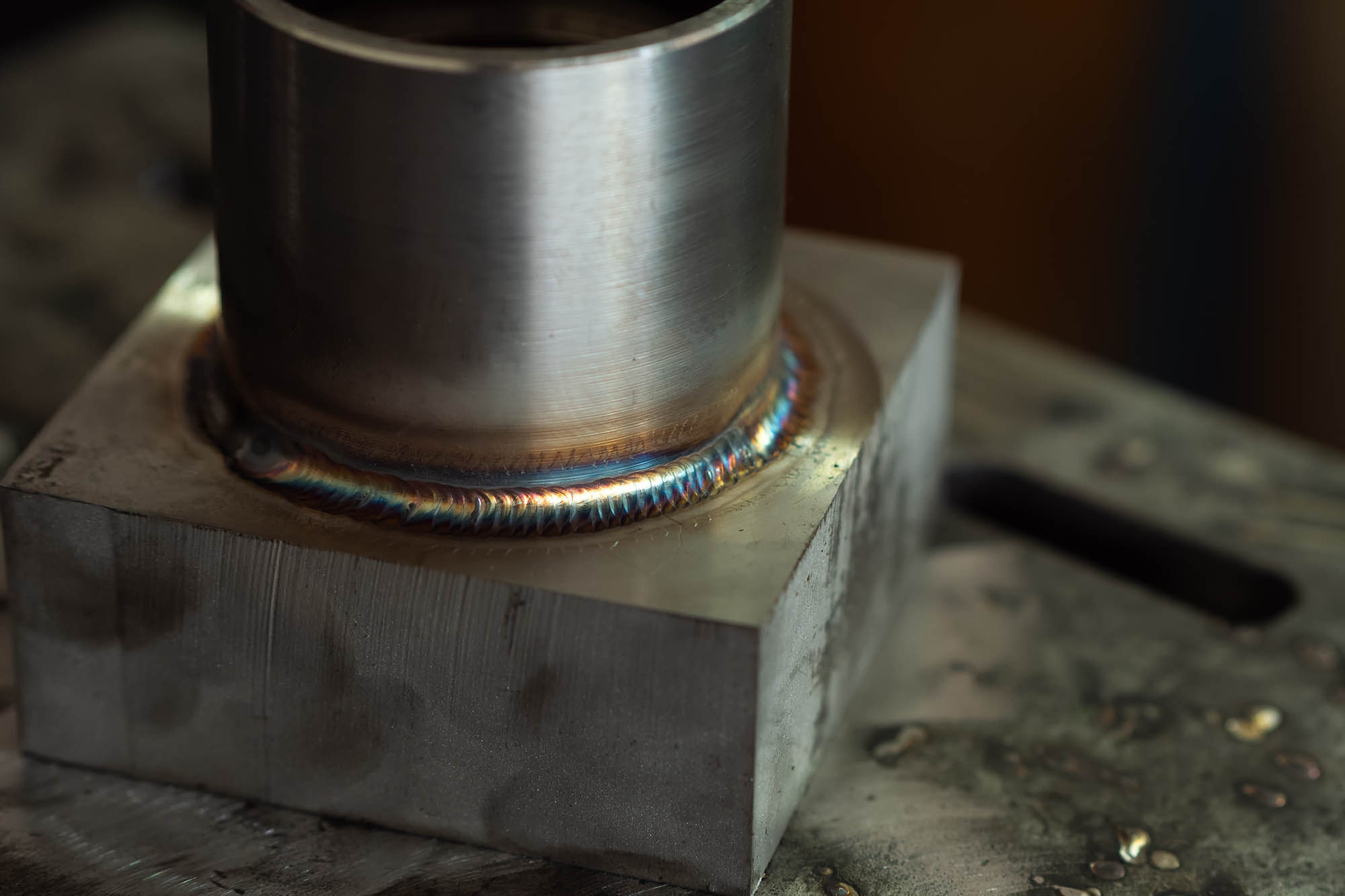
Factors Influencing Porosity Formation
The occurrence of porosity in welding is affected by a myriad of variables, varying from gas protecting efficiency to the details of welding criterion settings. One essential factor adding to porosity development is insufficient gas securing. When the shielding gas, normally argon or carbon dioxide, is not efficiently covering the weld swimming pool, climatic gases like oxygen and nitrogen can pollute the liquified steel, bring about porosity. In addition, the tidiness of the base materials plays a considerable published here role. Pollutants such as corrosion, oil, or dampness can evaporate throughout welding, creating gas pockets within the weld. Welding specifications, including voltage, current, travel speed, and electrode kind, additionally effect porosity formation. Using inappropriate setups can generate extreme spatter or heat input, which in turn can cause porosity. Furthermore, the welding strategy employed, such as gas steel arc welding (GMAW) or protected steel arc welding (SMAW), can affect porosity development as a result of variations in warmth distribution and gas coverage. Comprehending and managing these aspects are vital for minimizing porosity in welding procedures.
Results of Porosity on Weld Quality
The presence of porosity also weakens the weld's resistance to deterioration, as the caught air or gases within the gaps can react with the surrounding atmosphere, leading to degradation over time. Additionally, porosity can prevent the weld's capacity to stand up to pressure or effect, more threatening the general high quality and reliability of the bonded framework. In important applications such as aerospace, auto, or structural constructions, where safety and toughness are extremely important, the destructive impacts of porosity on weld top quality can have extreme repercussions, emphasizing the relevance of lessening porosity through correct welding methods and treatments.
Strategies to Reduce Porosity
To enhance the top quality of welded joints and make read this post here certain structural honesty, welders and fabricators utilize details methods aimed at decreasing the development of voids and dental caries within the material during the welding process. One effective approach to minimize porosity is to make sure correct product prep work. This includes thorough cleansing of the base steel to eliminate any impurities such as oil, grease, or wetness that can add to porosity development. Additionally, utilizing the suitable welding criteria, such as the correct voltage, present, and take a trip speed, is essential in avoiding porosity. Preserving a consistent arc length and angle during welding additionally helps decrease the probability of porosity.

Using the suitable welding technique, such as back-stepping or employing a weaving motion, can also assist distribute heat evenly and reduce the chances of porosity development. By applying these methods, welders can efficiently decrease porosity and generate top quality bonded joints.

Advanced Solutions for Porosity Control
Implementing cutting-edge innovations and cutting-edge techniques plays a critical duty in achieving remarkable control over porosity in welding processes. In addition, using advanced welding strategies such as pulsed MIG welding or customized environment welding can also assist mitigate porosity issues.
Another innovative service includes the usage of advanced welding devices. For circumstances, utilizing tools with integrated features like waveform control and advanced source of power can improve weld top quality and minimize porosity dangers. Additionally, the implementation of automated welding systems with accurate control over criteria can considerably reduce porosity problems.
Moreover, incorporating advanced tracking and evaluation modern technologies such as real-time X-ray imaging or automated ultrasonic testing can help in identifying porosity early in the welding procedure, enabling prompt rehabilitative activities. On the whole, integrating these click here now innovative remedies can substantially boost porosity control and improve the overall quality of bonded elements.
Verdict
In verdict, comprehending the scientific research behind porosity in welding is vital for welders and producers to generate top quality welds - What is Porosity. Advanced services for porosity control can further boost the welding process and make sure a strong and reliable weld.